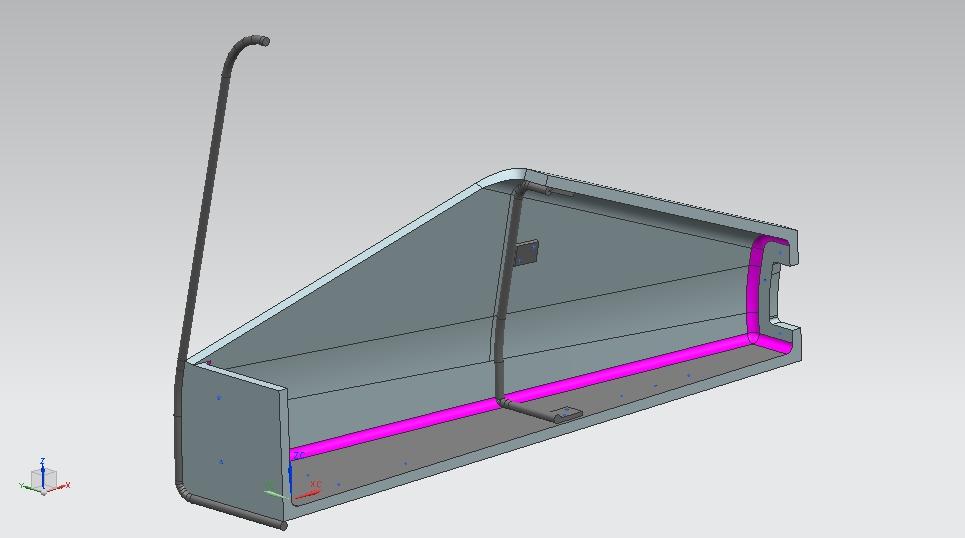
Published: 20-12-2015
My final year university group project was to design and test a composite monocoque for the university's Formula Student car. Lots of credit for this work needs to go to my group members, Tom Gough, Joe Edwards, and Anton Kasyanich. The full report can be found here and contains all the nitty gritty bits of information. For the sake of staying awake we'll skip some of the technical bits and dive into the more practical side of things for these articles.
So, what is Formula Student?
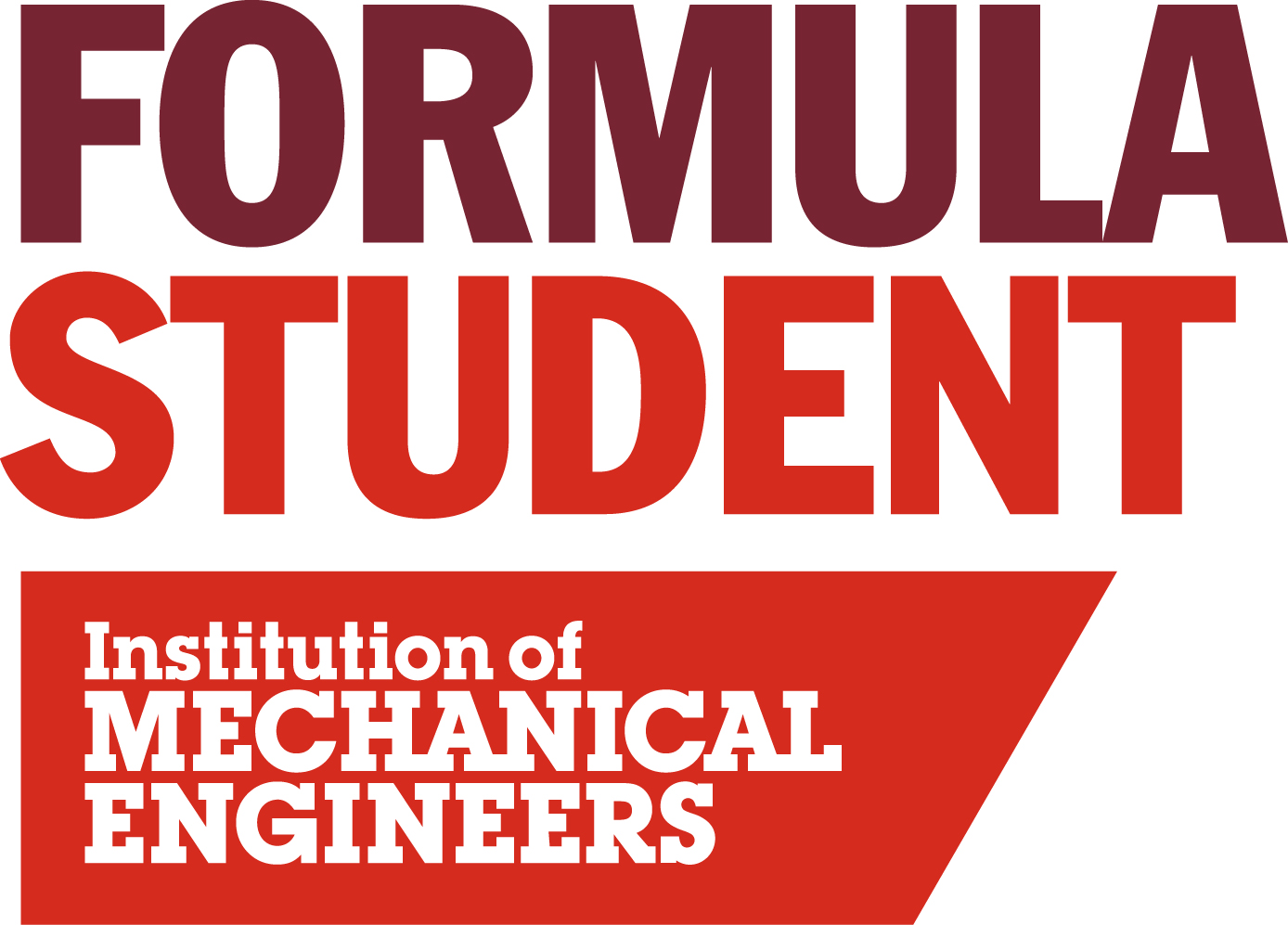
Formula student UK is an annual motorsport competition organised by IMechE for university students. Teams are required to design, test and build a single seater race car that satisfies the regulations. The competition is made up of static and dynamics events and is held at Silverstone during July over the course of five days. Cars must pass scrutineering in order to compete in the dynamic events. Scrutineering involves a technical inspection of all systems to ensure the cars satisfy the rules and meet safety requirements.
Every year SUFST, the Southampton University Formula Student Team designs and manufactures a single seater race car for participation in the UK Foromula Student Competition. 2015 was the third successive year a car was built for the competition. All cars have so far been entered into class 1. The GDP team aimed to work with SUFST helping to develop their future ideas and concepts.
Why a composite monocoque?
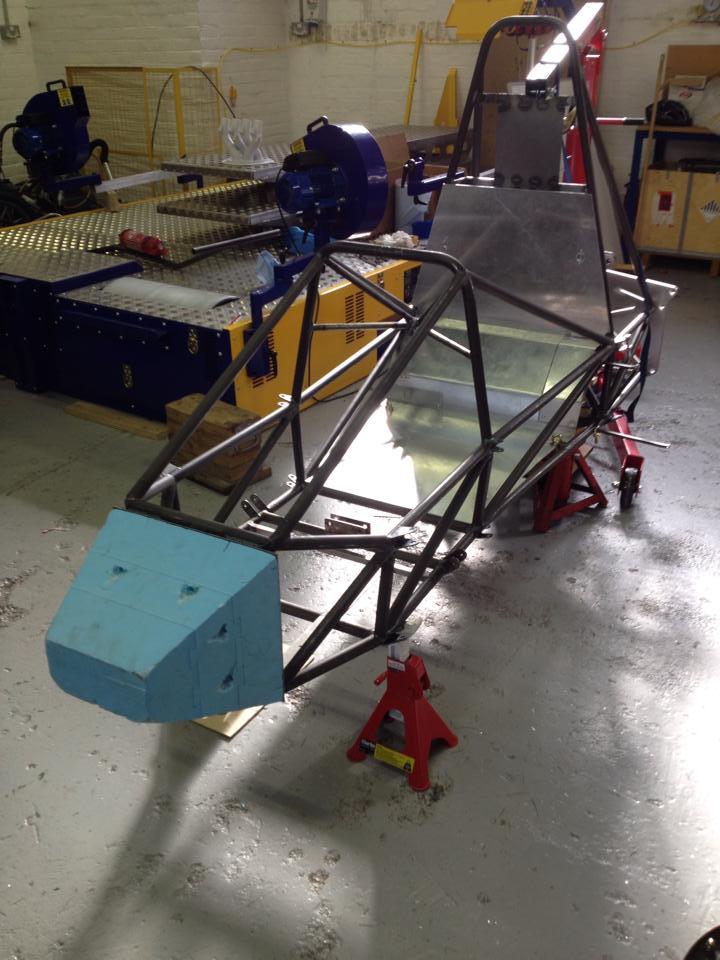
For severals years SUFST had used a steel tube space frame chassis due to the ease of construction and the flexibility it provides for design changes. They were however looking to construct a composite chassis to increase their competitiveness. A composite chassis can theoretically be lighter while offering increased strength and stiffness over a space frame, which is of great benefit to a race car. Designing a composite chassis however is difficult and requires fairly advanced modelling, testing and manufacturing skills, as well as a strict design regime.
Considering this, SUFST had asked the GDP team to carry out relevant research into a composite chassis. This was to be followed by the construction of a prototype which aimed to de-risk future implementations. A notable limitation is that a majority of the construction must take place in-house and this restricted the use of some advanced manufacturing techniques.
Project aims and objectives
The main aim of the project was to determine the feasibility of designing and manufacturing a composite chassis for a Formula Student car. It should be able to be manufactured at the University and not rely substantially on outsourced equipment or work. The objectives for this project include:
- Design a composite chassis which conforms to Formula Student Regulations (i.e. suspension pickup points, engine mounting points, driver positioning).
- Simulate the structural mechanics using FEA.
- Validate the FEA by testing material specimens as required by Formula Student rules.
- Construct a scale model to evaluate the manufacturing techniques.