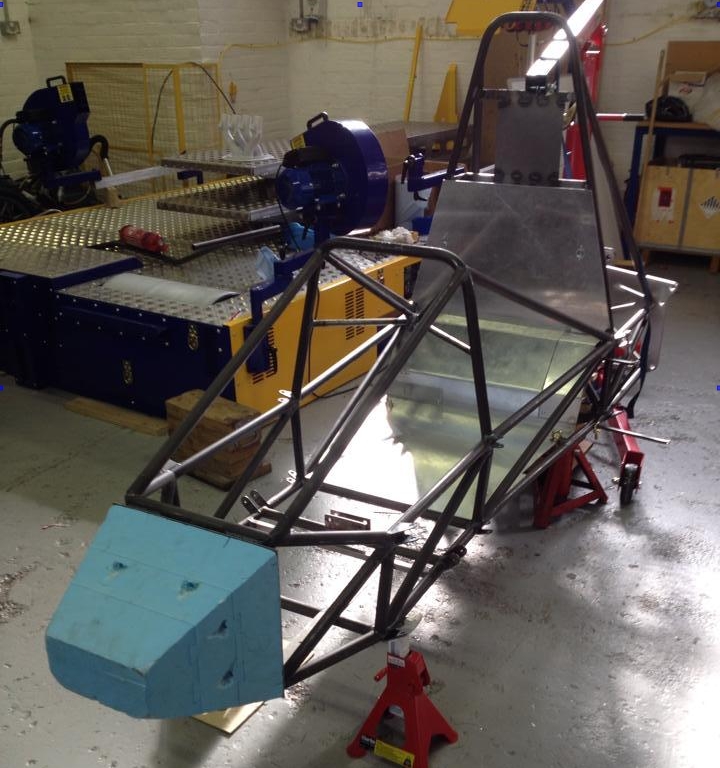
Published: 21-12-2015
Available resources
The resources available to the team influence the design and manufacturing techniques used. Notable equipment and facilities available to the team include:
- EDMC, specialists in manufacturing metal items
- Woodworking shop
- Laser cutters
- Resin infusion and vacuum bagging facilities
- Testing machines
Notable equipment and facilities not available to the team include:
- Autoclave capable of curing a full size car
- Large CNCing machine
Composite construction and race cars
What is a composite?
A composite material is simply a material composed of two or more materials. In this case a fibre and thermosetting plastic matrix.
Sandwich panels
A sandwich panel consists of a lightweight 'core' sandwiched on either side by a thin stiff skin. Common choices for the core are aluminium honeycomb, lightweight woods and foam. Fibre reinforced plastics are often used as the skin but aluminium and thermoplastics are also used. Sandwich panels are used for their exceptional strength to weight ratio under certain loading scenarios.
Manufacturing options
There are many different ways of manufacturing fibre reinforced plastics. Some of the most common processes that could be used are:
- Wet layup with/without vacuum bag
- Resin Transfer Moulding (RTM)
- Prepreg - Autoclave Cured
- Out Of Autoclave (OOA) Prepreg - Oven Cured
The best results are often achieved using an autoclave. Although the group did have access to an autoclave which was large enough to cure smaller specimens the decision was taken not to use this method as a full size at panel could not be manufactured this way. The same argument applied to out of autoclave prepreg. RTM, in particular resin infusion was chosen due the superior quality of laminate achievable over wet lay up. It provides a laminate with very low void content and high fibre volume
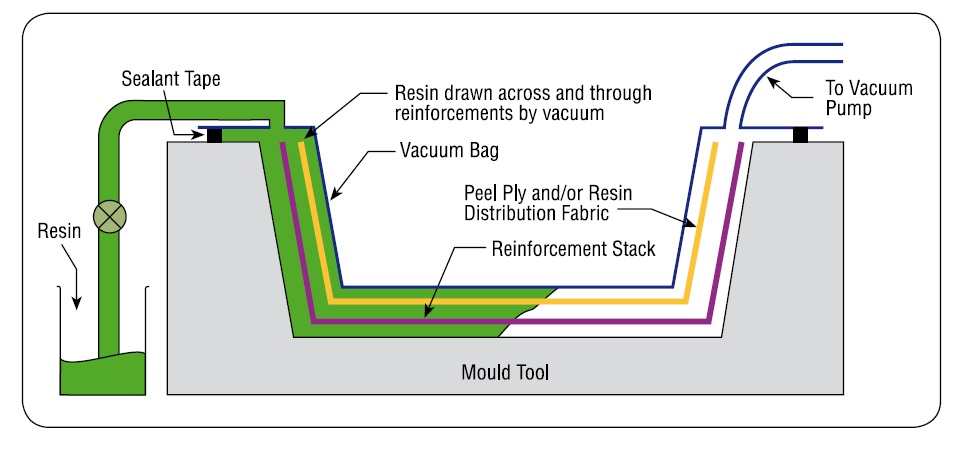
Resin infusion is a type of Resin Transfer Moulding RTM where the upper mould is eliminated and replaced by a vacuum bag. Typically the following steps are involved when creating a laminate using resin infusion:
- A release agent is applied to the mould. This could be a chemical release agent or wax and PVA combination.
- The dry fibre layers are then laid into the mould in the desired orientations.
- Peel ply is placed over the fibres to protect them and create a good bonding surface.
- Infusion mesh is placed over the peel ply, this helps the resin diffuse through the laminate.
- The resin inlet and vacuum lines are then placed in the correct positions.
- A vacuum bag is used to cover the stack and is sealed to the moulds flange using sealant tape.
- A vacuum is pulled using a pump and the resin is allowed the ow into the stack infusing the fibres.
- Once full impregnated the resin ow is stopped and the laminated allow to cure under vacuum.
Rules and regulations
In order to prove the chassis is structurally sound and safe it must pass tests defined in the Formula Student rules. All results and necessary information are used in the scrutineering process. A composite chassis is subjected to a different and more stringent set of rules compared to a space frame chassis. They require physical testing to prove strength and stiffness. The aim of these rules is to prove that the composite chassis is at least as strong and safe as an equivalent steel space frame chassis.
Designing a chassis for Formula Student
Designing a race car starts with the tyres. Once the tyres are chosen and all relevant data is known the suspension is designed to make best use of them depending on what the team wants from the car in terms of vehicle dynamics. The chassis is then designed around these suspension points, powertrain unit and the drivers cell. It is used to interlink all the component that make up a race car and transfer the loads effectively.
A typical track at a formula student event is tight and twisty with cars often averaging around 35 mph. This type of track used lends itself to specific suspension geometry. Short-long arm suspension is almost always used as it offers good performance. [10, p.627] Parameters such as caster, camber and king-pin angle are optimised for the desired handling characteristics and this helps resolve the location of the chassis connections.
One of the most import characteristics of a chassis is its torsional stiffness. Torsional stiffness is a measure of the resistance provided by the chassis to twisting. A stiff chassis is key to be able to design and predict the handling characteristics through the suspension and steering systems. When a chassis is relatively exible its ability to control lateral load transfers is unpredictable and so difficult to set up and control. Lateral load transfer is the transfer of load from the inside wheels to the outside wheels. [10, p.678]
Suspension and steering considerations
When designing a Formula Student chassis, suspension and steering hard points play a major role in the shape and strength required in certain areas. Although the suspension and steering geometry will not be considered in huge detail and optimised it must be thoroughly accounted for in order to create a realistic design with appropriate load paths. Limitations a cut and fold composite chassis has on suspension design will be the primary focus of the research.
Chief judge of FSAE Australasia and Germany, Pat Clarke has written many technical articles detailing FS car design. In one he describes beneficial suspension and steering characteristics and parameters for a FS car [12]. It describes the following as beneficial:
- Camber control when the chassis rolls is critical.
- Camber gain at the suspension is desirable but the effects of King Pin Inclination (KPI) and Caster should be taken into account.
- Good design have lots of caster but not much KPI.
- Bump steer should be avoided and tested for after any design changes.
- A large amount of positive ackerman is good.
- Camber should never go positive on a loaded wheel while cornering.
- Roll steer is not wanted.
- Stiff suspension rates, aggressive anti dive and anti squat geometry are not needed (unless making use of aerodynamics) and compliant suspension rate may provide more mechanical grip if wheel angles are controlled.
- Design should ensure good control of the roll centres.