Frame
The first job was to design a suitable frame. Aluminium extrusion profiles seemed to be commonly used by a lot of other CNC DIYers. It provides a really modular and easily to align structure. No drilling is required (perhaps a bit of tapping) and it can be ordered to length ready to be put together, perfect. After sketching the rough dimensions (3m by 1.5m) and having a look for seller online I found the down side, PRICE. This stuff is expensive and it instantly put me off. I needed £500+ of it! The price of steel looked very enticing now.
After spending a few days checking out steel, vanilla aluminium and the aluminium profiles I decided that the extra work required to drill and possibly weld the vanilla steel and aluminium wasn't worth it, not for my first build anyway. I simply don't have access to the necessary tools to do it accurately enough. Maybe once this machine is done it can be used to help create a nice stiff steel machine. For now buy and bolt together is fine :) Below are a few images of my first go at a basic structure. They also show positioning of the angle iron and v wheels that will be explained below.
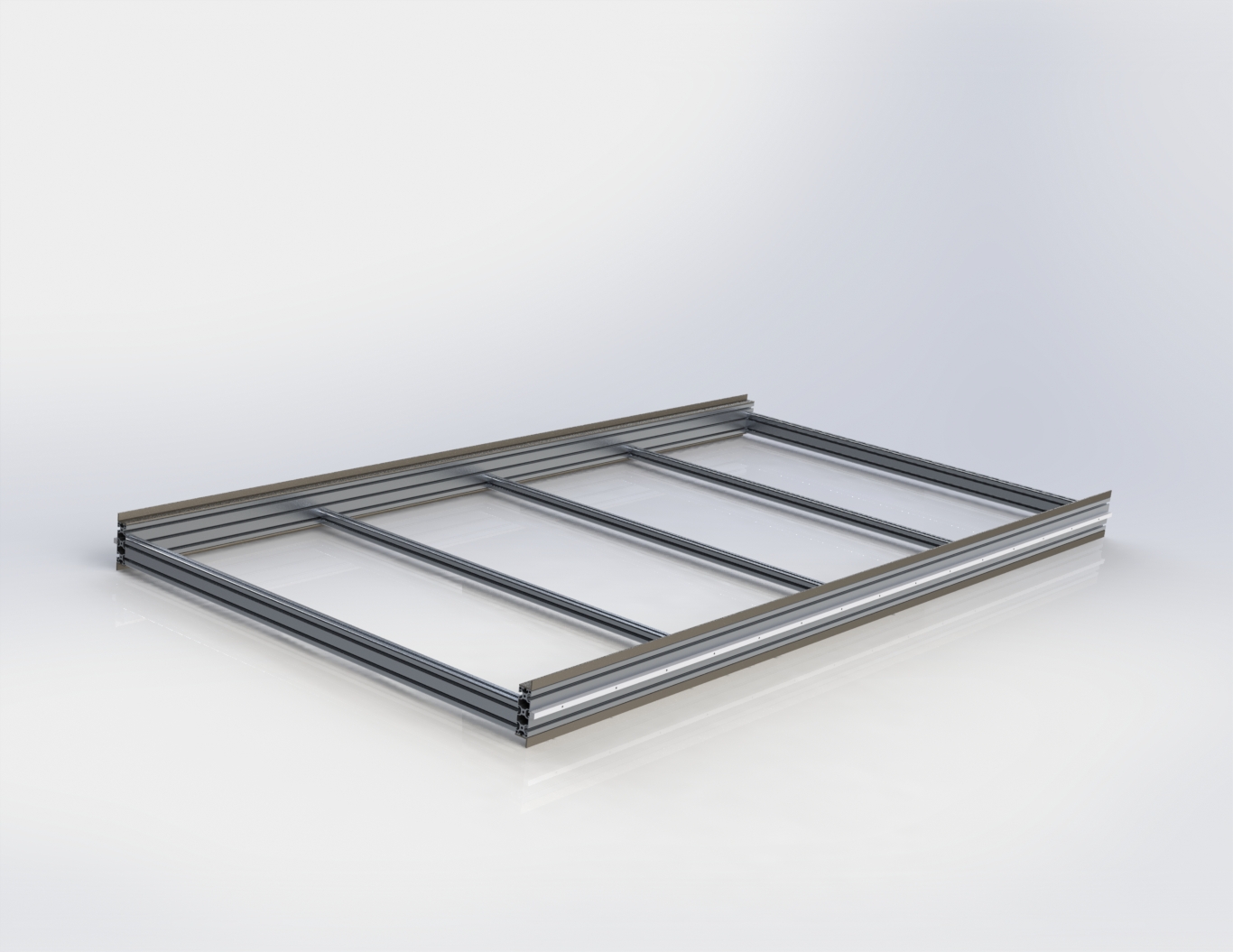
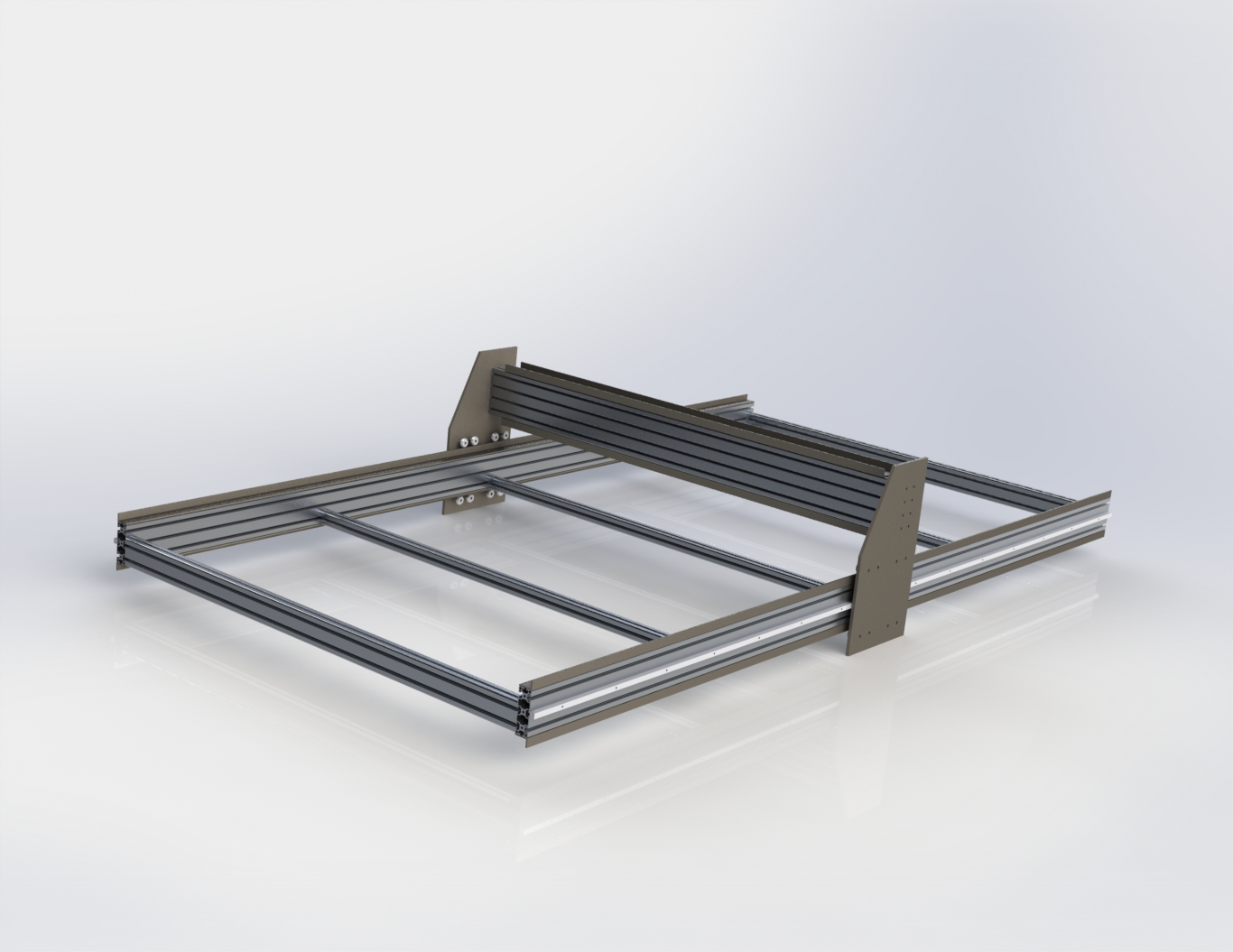
Linear motion
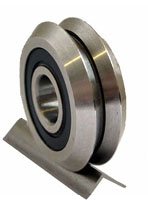
The next job is to design the linear motion system. The gantry and Z-axis must be able to smoothly and securely move while coping with the cutting loads. The various different methods of attaining linear motion were discused in part 1 and it was decided that v-groove bearings and rails were the way to go.
Professionally hardened steel v-groove rails are expensive (ridiculously) and so 4mm thick angle iron was substituted. From a few other builds including this I had seen that after wearing in, angle iron seemed to perform okay as a v rail. For 5-10% of the price of the professional steel v rails I had to try it out. If they don't perform as expected a v shape will be cut into the angle iron.
The v bearings themselves are also slightly expensive compared to standard flat bearings (think skateboard bearing) but they are reasonable. They are also meant to perform better in dirty environments as they kind of self clean. All in all you can get them for ~ £3-4 each if you import them from china or in some cases the USA (check Ebay out). Supplies in the UK seem to be non-existent or just very hard to find using Google. Eight of the v bearings are to be used on each side of the gantry. The bottom row will have eccentric spacers so they can be tightened on the rail.
Linear drive
Various types of mechanical motion were looked at in part 1 including the use of ball-screws, belt drives, chain drives and the rack and pinion. Due to the 3m length of the table, rack and pinion was chosen as the most suitable. It also has the added benefit of possibly having multiple gantries that operate independently of each other in the future. I.E A router gantry for cutting wood/aluminium and a hotwire gantry for cutting large block of foam.
The cheapest smallest rack I could find is of size MOD1 (15mm square). It works out at ~£150 for 3m (pre-drilled). Expensive but should be worth the money. The particular one I am looking at is from here and is pre-drilled, super handy for me.
The next problem is how to drive it. The stepper motor will be mounted on the gantry plate. From this position direct drive is easiest but not idea. Ideally the motor should have some kind of geared reduction either by gearbox or belt. A belt reduction requires extra mechanical structure but is fairly cheap. Buying a motor with an attached planetary works as a 'drop in' replacement. They are however more expensive than a belt reduction and have a high tendency to lose accuracy with extended use. Trying to keep the build simple a planetary gearbox will be used.
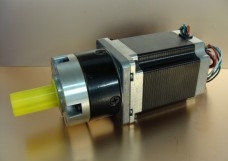
Z-axis
Not much thought has been put into this yet. Ironically this is one of the most important parts of the machine. As the the only fully cantilevered structure on the machine it must be strong and appropriately sized. Might just buy a ready made one.
Electronics
Kits are not hard to come buy. Generally these included a power supply, microstepping drivers and the motors. Nema 23's should suffice for this build.