
Published: 26-12-2015
Introduction
This series of articles document some of the work done during 2013/14 for the Southampton University Formula Student Team SUFST. As the Head of Aerodynamics & Bodywork it was my responsibility to lead the design and manufacture of the external surfaces. This involved using CAD and CFD software for design and simulation. Knowledge of composite structures was also required to manufacture the final parts.
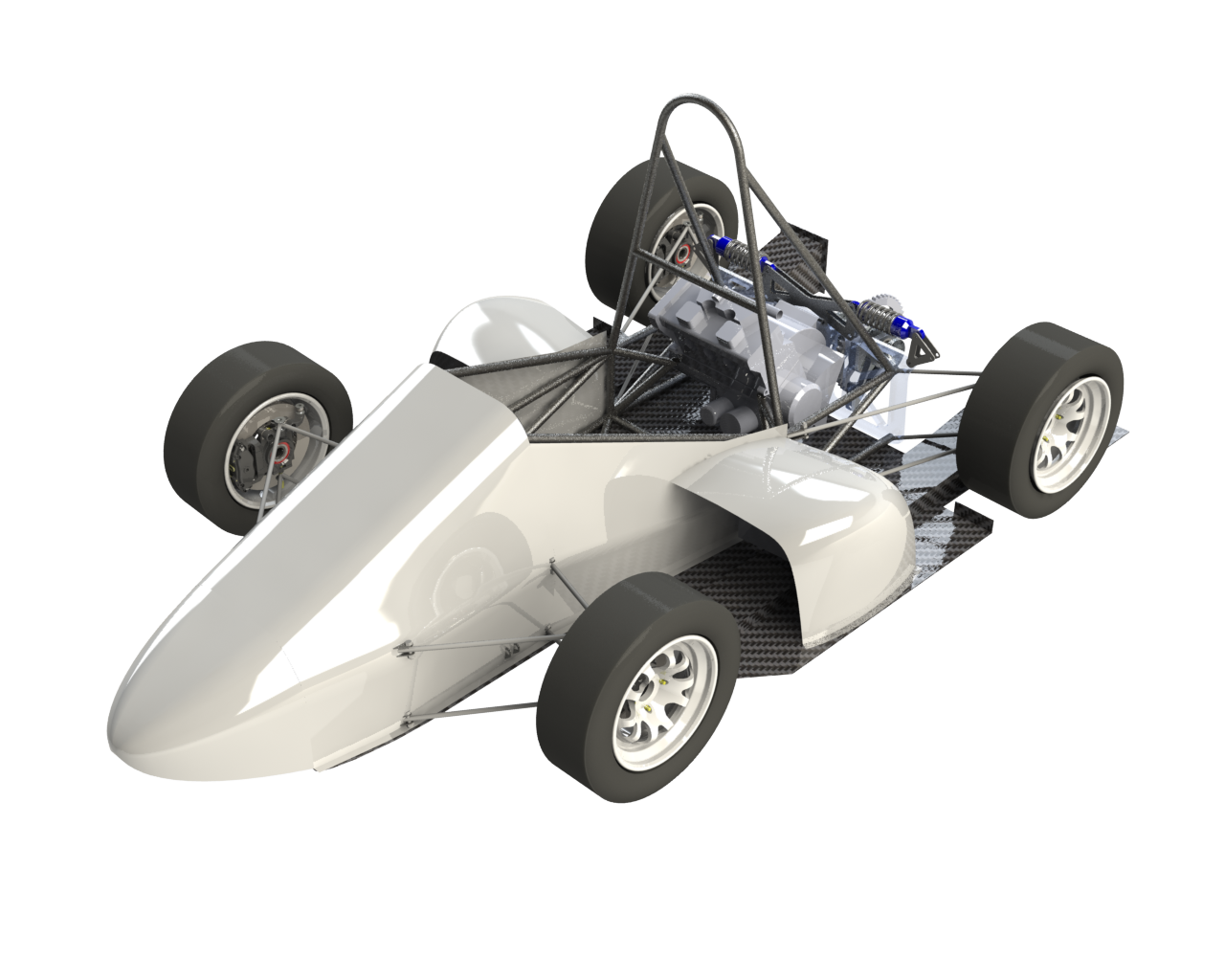
Initially the design included sweeping bodywork and an aerodynamic underfloor. The underfloor was however dropped towards the final parts of the process due to time and money constraints. A flat panel would replace the profiled underfloor and provide support for the radiator shrouds. The parts (shown in an exploded view below) were designed to be easily demountable. The two sides would be permanently attached to the car and mounted before the suspension is attached. They have a curved lip and 'sit' on the flat floor. the rest of the panels then lock into the side panels for a flush fit.
Manufacturing Considerations
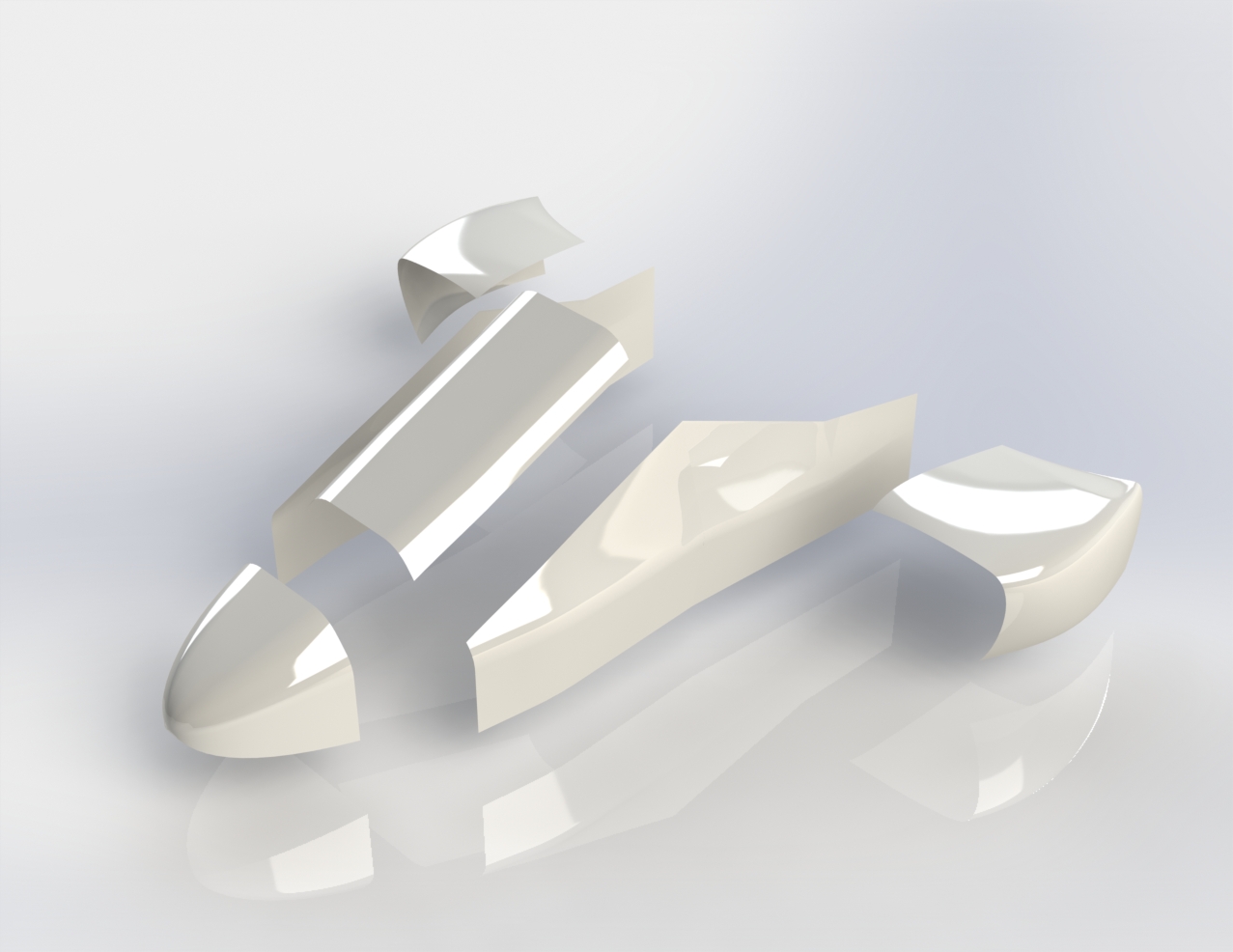
Initially the design included sweeping bodywork and an aerodynamic underfloor. The underfloor was however dropped towards the final parts of the process due to time and money constraints. A flat panel would replace the profiled underfloor and provide support for the radiator shrouds. The parts (shown in an exploded view below) were designed to be easily demountable. The two sides would be permanently attached to the car and mounted before the suspension is attached. They have a curved lip and 'sit' on the flat floor. the rest of the panels then lock into the side panels for a flush fit.